Пеллеты – современное эффективное топливо для отопительных печей и котлов. Они дают больше тепла, чем дрова, но главное достоинство пеллет в другом. В отличие от дров, их можно автоматически дозагружать в печь или котел, поэтому отопление требует гораздо меньше ухода, чем дровяное. В зависимости от типа печи или котла и объема бункера, срок работы с одной загрузки пеллет составляет 5–10 дней. Главный недостаток пеллет – высокая цена, по этому параметру они в 3–5 раз дороже дров или угля, если сравнивать не по объему, а по производимому теплу. Поэтому самостоятельное производство пеллет позволит серьезно сэкономить, ведь в качестве материала можно использовать любые деревянные отходы.
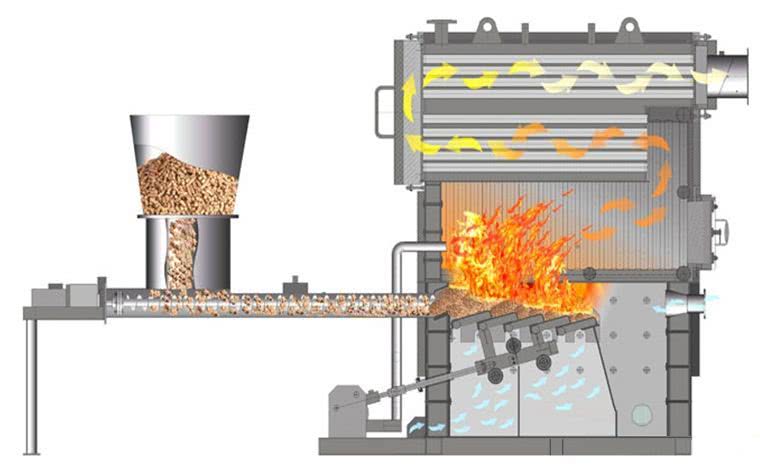
Как делают пеллеты
Технология изготовления пеллет проста – опилки продавливают через отверстия в матрице и обрезают ножом. Однако есть несколько условий:
- влажность опилок должна быть 11–13 %;
- давление не меньше 50 кг/с?;
- непрерывная подача опилок.
Поэтому для их изготовления потребуется:
- сушилка;
- влагомер;
- гранулятор.
Сушилка
Для создания сушилки потребуются 3 стальные бочки объемом 200 литров. У двух бочек вырезают по одной крышке, а у одной обе крышки. Внутри каждой бочки вставляют лопатки для пересыпания опилок. Длина лопаток 10–15 см, расстояние по окружности между лопатками 20–30 см. Ряды лопаток располагайте вплотную, лопатки ставьте так, чтобы между ближайшими лопатками соседних рядов было 8–15 см. Проще всего крепить лопатки на заклепках. В бочках с одной вырезанной крышкой необходимо прорезать отверстия размером 20х20 см, через них будет происходить загрузка и выгрузка опилок.
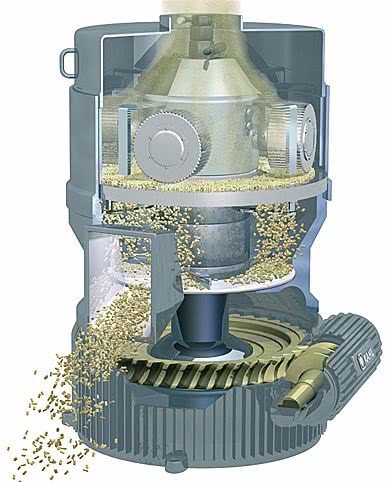
Затем все бочки нужно поставить одну на другую (бочки с отверстиями должны быть сверху и снизу), выставить их по отвесу и соединить между собой. Для этого можно использовать газовую сварку или электрический сварочный инвертор с электродами 1 или 2 мм. В торцах полученной конструкции вырезают отверстия диаметром 40–50 см, это будут вход и выход горячего воздуха. После этого делают вал и крепления. Для вала нужен ровный стальной прут длиной 3,5–4 метра и диаметром 20–50 мм. Его необходимо вставить внутрь конструкции строго по центру и прикрепить к торцам бочек стальными полосками шириной 20–30 мм и толщиной 4–6 мм. Вал должен одинаково выступать с обеих сторон конструкции.
Под этот вал изготовьте крепления произвольной формы, которые будут удерживать всю конструкцию на весу. Вал устанавливайте на подходящие по размеру подшипники качения или подшипники из бронзовых втулок. Если вы будете использовать бронзовые втулки, то в наружную врежьте ниппель для смазки, это продлит срок службы подшипника и облегчит вращение конструкции. К валу через редуктор присоедините мотор мощностью 1 кВт.
Редуктор должен обеспечивать вращение барабана со скоростью 5–15 оборотов в минуту. Желательно использовать мотор с возможностью регулировки оборотов, благодаря этому вы сможете точней подбирать режим сушки.
На входе конструкции установите бункер для опилок объемом 3–10 ведер. Низ бункера должен полностью повторять форму бочки. В этом случае отверстие будет играть роль дозатора. Меняя размер нижней части бункера и прорези в бочке вы сможете подобрать оптимальное для своих условий (размера и влажности опилок, скорости вращения вала, температуры входящего воздуха). В качестве источника тепла используйте электрическую или газовую тепловую пушку мощностью 3–10 кВт. Желательно использовать устройство с возможностью регулировки скорости подачи и температуры воздуха.
Работает сушилка так:
Измеряете влажность опилок.
- Загружаете бункер опилками (убедитесь, что отверстие не находится под бункером).
- Включаете тепловую пушку.
- Включаете электродвигатель, вращающий барабан.
- На выходе подставляете под барабан емкость для приема сухих опилок.
- Измеряете влажность подсушенных опилок.
- Если нужно, то повторяете сушку.
Для измерения влажности используйте влагомер, который продают в большинстве строительных магазинов. Влагомеры измеряют электрическое сопротивление опилок и на основании этого параметра определяют влажность. Стоимость недорогих моделей 3–7 тысяч рублей. Если есть возможность, берите влагомер с режимом выбора породы древесины, он выдает более точные результаты.
Гранулятор
Это устройство работает так же, как и гранулятор для сельхозкормов, разница только в давлении, которое создают колесики-шестеренки. Для его изготовления потребуются:
- стальная труба диаметром 30–50 см (можно использовать старый газовый баллон) и длиной 100–130 см;
- листовой металл толщиной 40 мм;
- электромотор мощностью 5 и более кВт;
- мощный редуктор;
- вал толщиной 20–40 мм;
- нож для деревообрабатывающего станка;
- различный металлолом.
Основные детали гранулятора – матрица и зубчатые колеса. Матрицу вы сделаете из толстого листового металла, а в качестве зубчатых колес можно использовать шестеренки одинакового размера. Оптимально подойдут зубчатые колеса и матрица от сломанного гранулятора для сельхозкормов. Вот последовательность действий для изготовления гранулятора:
- вырежьте из стали толщиной 40 мм круг диаметром чуть-чуть меньше внутреннего диаметра трубы (эту операцию удобней делать с помощью газового резака), это будет матрица;
- обточите диск, чтобы придать ему идеальную форму (круглый, с параллельными плоскостями);
- просверлите в нем отверстие под вал и бронзовую втулку;
- закажите токарю или сделайте сами бронзовую втулку в форме буквы Т, широкая часть нужна для опоры на матрицу;
- выберите в матрице посадочное место для втулки и убедитесь, что все детали подходят друг к другу;
- отступите от верхнего края трубы 10–15 см и приварите бортик, на который будет опираться матрица, если не сможете найти подходящего по диаметру стального кольца, то приварите кусочки размером 3х3х3 см, одна сторона которых обточена по форме трубы;
- эту операцию выполняйте точно, потому что отличие по высоте установки любого из кубиков хотя бы на 0,5 мм снизит эффективность работы всего агрегата;
- сбоку прорежьте в матрице паз для замка и приварите подходящий по размеру кусок стали к любой стенке, надев матрицу на него, вы обеспечите ее неподвижность;
- под местом для установки матрицы вварите желоб, по которому готовые пеллеты будут выходить наружу и прорежьте отверстие для их выхода, размер отверстия 10х10 см, желательно, чтобы желоб выступал из корпуса хотя бы на 30 см;
- установите в нижней части трубы редуктор;
- присоедините к нему вал и выберите места для двух подшипников, один неподалеку от редуктора, второй немного ниже желоба;
- закажите токарю шайбы для фиксации подшипников – внутренний диаметр на 0,03 мм меньше диаметра вала, наружный на 8 мм больше диаметра вала, толщина 8 мм;
- нагрейте газовой горелкой одну из шайб до красного цвета и наденьте на вал, доведите до места установки подшипника и зафиксируйте там чем-нибудь, когда шайба остынет, то надежно будет держать подшипник;
- наденьте на вал подшипник и зафиксируйте второй шайбой, таким же образом закрепите и второй подшипник; закажите токарю ось колесиков, она должна надеваться на вал сверху и фиксироваться шпонкой и двумя гайками;
- вал отдайте фрезеровщику, чтобы он прорезал посадочное место под шпонку и нарезал резьбу под гайки;
- приварите к валу ниже матрицы нож для обрезки пеллет, его можно сделать из ножа для фуговочного станка, не перепутайте направление ножа, иначе он будет не резать, а мять пеллеты;
- подключите к редуктору электрический или бензиновый мотор;
- соберите всю конструкцию и убедитесь, что ничего не напутали и можете регулировать высоту колесиков; снимите колесики и матрицу;
- просверлите в матрице отверстия, диаметр отверстий зависит от размера опилок или стружки – для мелких опилок 3–4 мм, для крупных 4–5 мм, а для стружки 5–8 мм, отверстия сверлите по траектории движения колесиков, расстояние между отверстиями в любом направлении должно быть в 3 раза больше их диаметра;
- установите в дрель сверло, диаметр которого в 2 раза больше и раззенкуйте им отверстия с лицевой стороны матрицы, это необходимо для создания нужного давления во время обработки опилок или стружки; зашлифуйте наружную поверхность матрицы, затем закалите ее;
- из металла толщиной 1 мм сделайте загрузочный бункер объемом 2–3 ведра и установите в него задвижку, чтобы регулировать скорость подачи материала;
- сверху установите на трубу загрузочный бункер (крепите его только на болтах, иначе сложно будет обслуживать агрегат); проверьте, правильно ли вы все собрали;
- включите гранулятор и засыпьте в бункер опилки;
- если пеллеты покажутся вам недостаточно плотными, отключите мотор, дождитесь его остановки и сильней прижмите колесики к матрице, помните, вал должен вращаться с небольшим усилием и легко поворачиваться даже двумя пальцами;
- если снова плотность пеллет недостаточна, потребуется новая матрица с меньшим диаметром отверстий.
Вывод
С помощью такого оборудования вы сможете самостоятельно производить пеллеты, которые гораздо лучше подходят для котлов длительного горения, ведь их можно догружать в топку автоматически, без остановки котла или печи. Расходы на электроэнергию или топливо для моторов не идут ни в какое сравнение с той экономией, которую вы получите, отказавшись от готовых пеллет и производя их самостоятельно.