Ниже приводятся сравнительные прочностные, деформативные и другие свойства неармированных и армированных шлакощелочных и портландцементных бетонов при кратковременном и длительном загружении.
Наиболее широко в строительстве применяются бетоны марок 300—500. В исследованиях использованы шлакощелочные бетоны марки 300 на мелкозернистом и марок 300 и 500 — на крупном заполнителе.
По составу эти бетоны не являются оптимальными, так как главной задачей являлось определение возможных пределов свойств бетонов и факторов их определяющих.
Поэтому в виде дисперсных заполнителей использовали некондиционные мелкие пески с содержанием пылеватых и глинистых частиц, превышающим требования ГОСТ, и применяли пластичные бетонные смеси.
Для приготовления мелкозернистого шлакощелочного бетона состава 1 применяли следующие материалы: овражный песок с содержанием глинистых и пылевидных частиц 13,3%; днепродзержинский гранулированный шлак, размолотый до тонины, характеризующейся удельной поверхностью по ПСХ-2 — 3000 см2/г; в виде щелочного компонента использовали кальцинированную техническую соду по ГОСТ 10689—70 в виде водного раствора с ?=1,2 г/см3.
В качестве вяжущего для крупнозернистых шлакощелочных бетонов применяли запорожский доменный гранулированный шлак с тонкостью помола 3000—3500 см2/г и щелочной компонент: для составов 2, 4, 5 — кальцинированная сода с той же плотностью, а для состава 3 — силикат натрия (натрий кремнекислый мета) по ГОСТ 4239—66 с плотностью раствора ?=1,08 г/см3.
Вяжущим для обычных бетонов составов 6 и 7 служили портландцемент марки 500 бахчисарайского комбината «Стройиндустрия».
Для крупнозернистых бетонов обоих видов заполнителями использовали: песок кварцевый с Мкр=0,985 и карбонатный щебень крупностью 10—20 мм.
Расход материалов на 1 м3 бетонной смеси приведен в табл. 31.

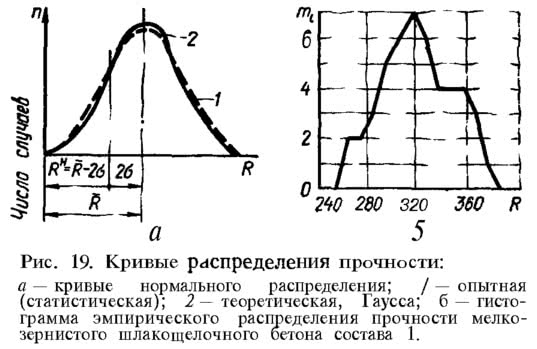